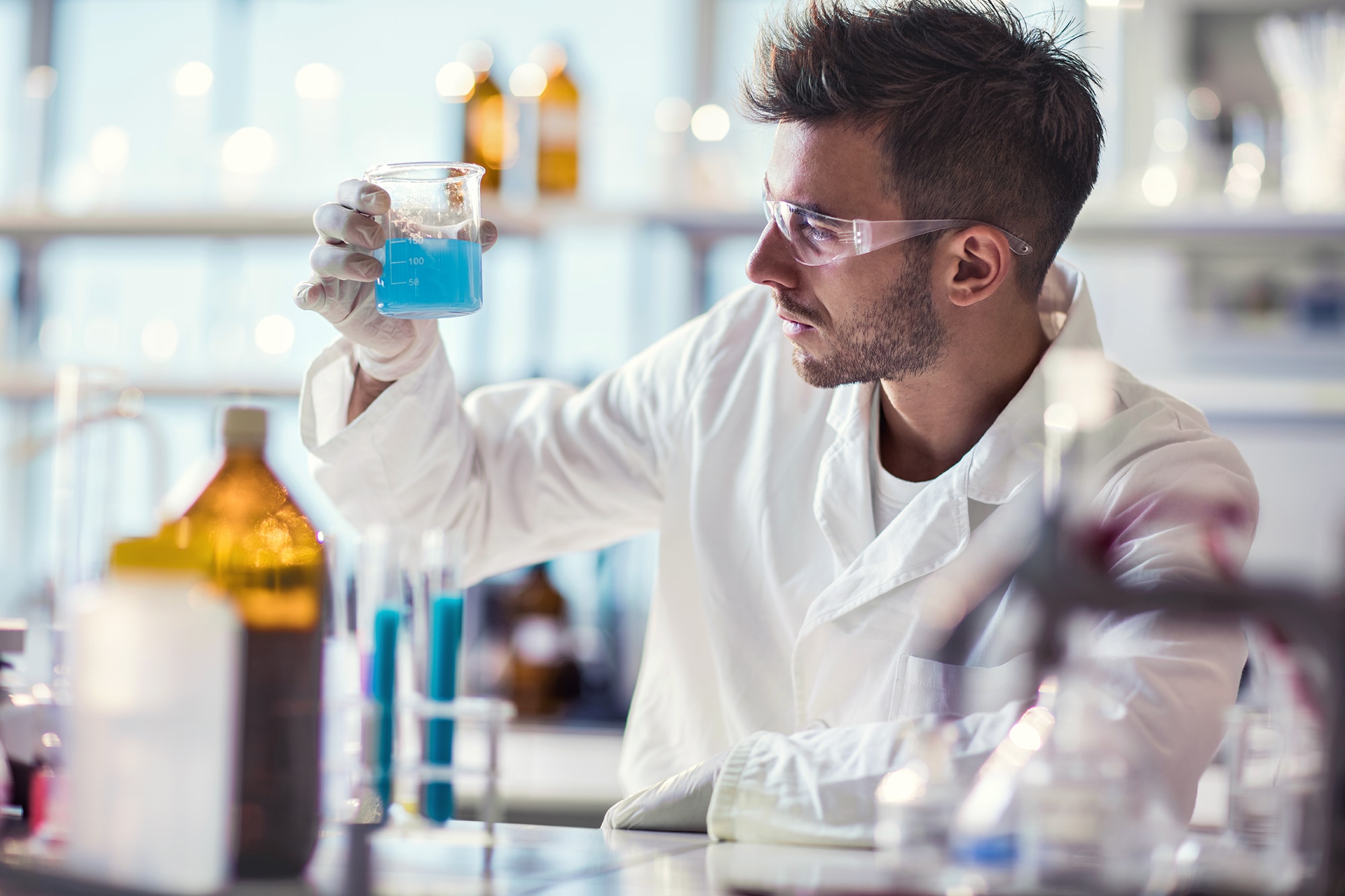
Most nylons and polymers begin their lives as pellets and powders before being molded into shape with heat and pressure. Cast nylon 6 skips this step by undergoing a casting process that provides unique advantages in performance and processing. Going straight to its final form eliminates extra heat histories, maximizing molecular weight and improving wear, abrasion, and fatigue resistance.
How Does the Casting Process Work?
Cast nylon 6 starts with three key ingredients:
- Caprolactam (nylon 6 monomer)—A solid at room temperature that turns liquid at 300°F
- Catalyst—Controls reaction speed and molecular weight
- Initiator—Triggers polymerization when combined with monomer and catalyst
All three ingredients remain stable until they’re brought together. Once mixed, the material begins to grow in molecular weight and solidify into a polymer, with casting times ranging from five to 30+ minutes. The speed of solidification depends on the relative amounts of catalyst and initiator as well as temperature and humidity conditions.
Flexible Casting Options
A. Static casting—Ideal for large, thick-walled parts
B. Spin casting—Produces round or cylindrical shapes
C. Smartcast* solutions—Combines the strength and wear resistance of Nylatron™ cast nylon with more efficient production and improved precision
*Trademark pending
![]() |
Your partner in cast nylonMitsubishi Chemical Group offers the widest range of cast nylon solutions. |
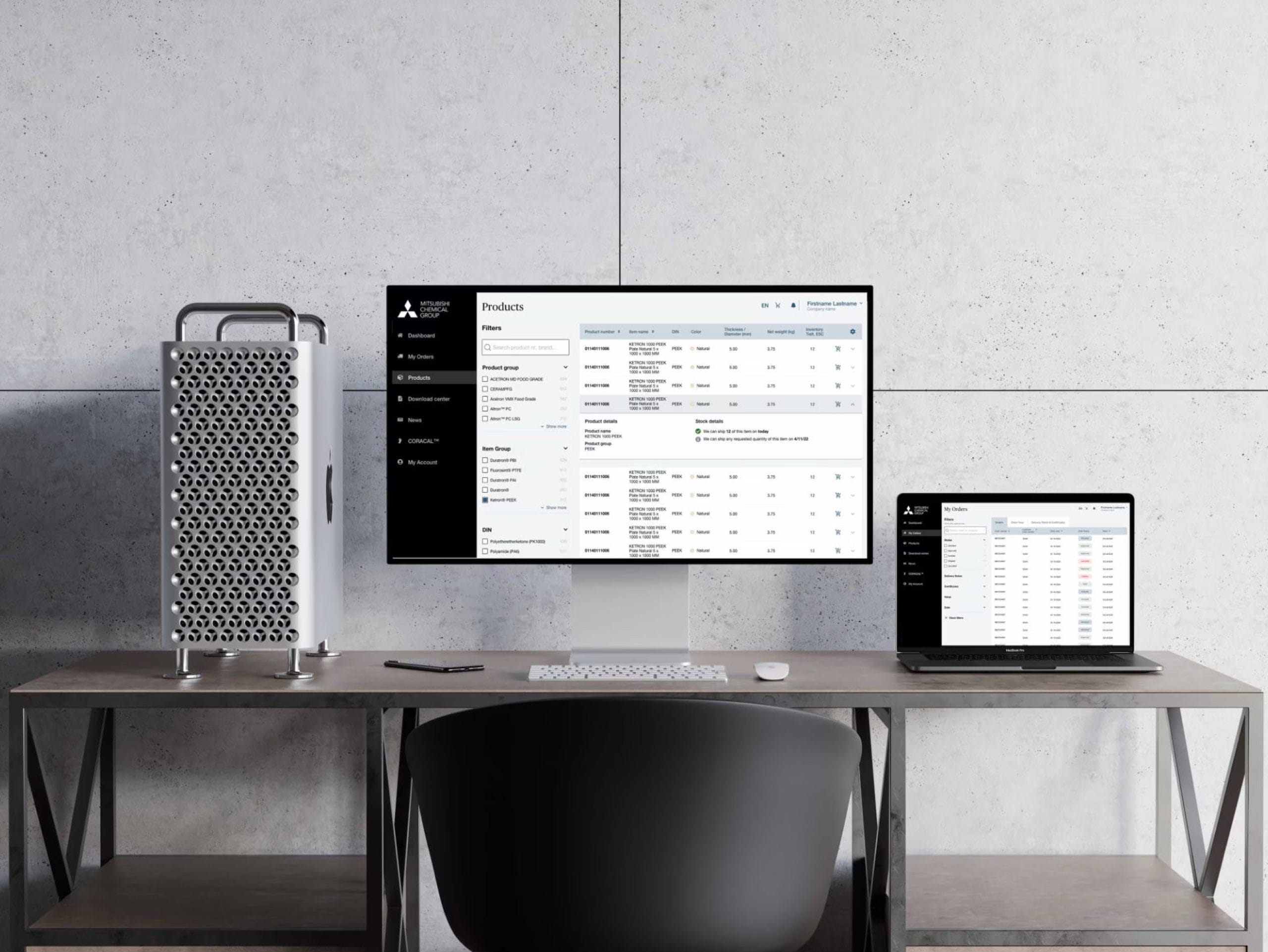
Simplify Your Workflow with MCAM Connect
Easily manage orders, access critical data, and get tailored support — all from one powerful platform.